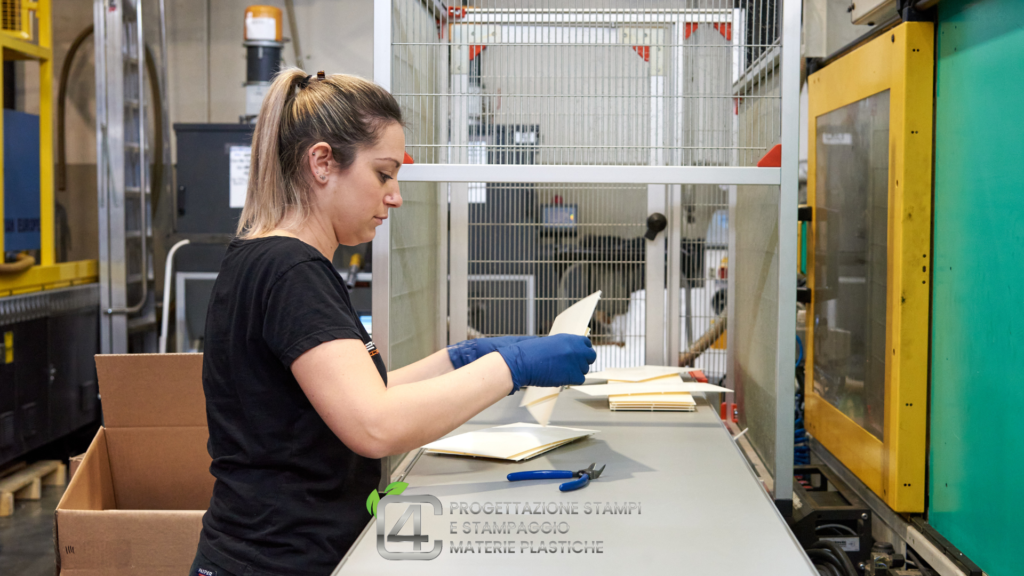
Introduction to injection molding
Injection molding is a technique used in the production of many plastic objects, from the simple plastic fork to car interior elements. Through this process, molten plastic material is injected into a mold, cooled and then extracted as a finished product.
The injection molding technique dates back to the 19th century and, with the advent of modern technologies, has become one of the main manufacturing methodologies for a wide range of products.
All injection molding operations are carried out within 4C Srl with the most modern technologies available to guarantee the quality of the finished products for our customers but also to guarantee safety for all our operators involved in the various phases.
The injection molding process
Material preparation and design
It all starts with mold design.
Thanks to modern CAD technologies, molds can be designed with millimeter precision and according to precise customer specifications.
Injection cycle
During this phase, the transported plastic material is heated until it becomes liquid, it is finally transported to the processing area by our distribution system and then injected into the mold under high pressure, it is an extremely delicate phase supervised by expert collaborators.
Cooling cycle
After injection, the material begins its cooling process, taking on the final shape of the mold.
Extraction of the final product
Once the product has solidified, it is removed from the mold and here we have our final object, ready for shipping.
It is easy for the process just completed to be repeated several times to obtain not only a single product but a larger batch, always at the discretion and upon request of the customer who requested it.
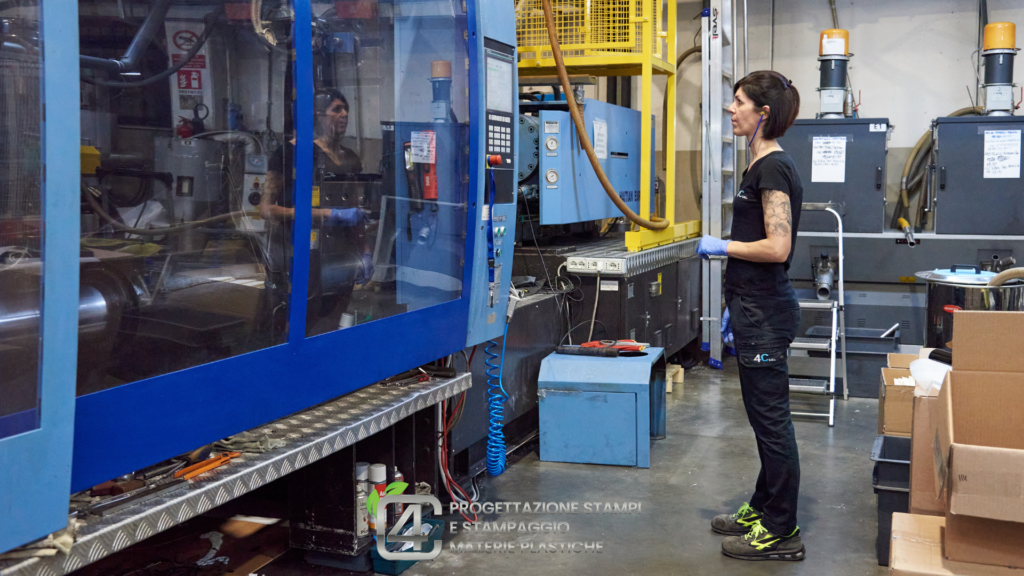
Advantages of injection molding
High efficiency and productivity
One of the main advantages of injection molding has always been its efficiency: once the mold has been created, it is possible to produce large quantities of product from the same mold in a short time and with the minimum margin of error and burrs.
Versatility in design
Injection molding but above all the creation of the mold tailored to the customer's specifications allows you to create products with intricate and complex details, offering a wide range of design possibilities, perfectly functional for the customer who requests their creation.
Cost reduction
The ability to produce in mass leads to a significant reduction in production costs per unit, in 4C Srl the single product can weigh up to 3 kg or be of minimal weight, in both cases the production costs thanks to the distribution of plastic materials and the constant updating of the machine park is optimized for full customer satisfaction.
Environmental sustainability
4C Srl supports and guarantees the circular economy path and with the use of recycled materials and the reduction of waste, injection molding is a more sustainable process than other techniques on the market.
Conclusions
The art of injection molding has revolutionized the world of manufacturing, offering efficient, economical and sustainable solutions. For those looking to combine quality, efficiency and sustainability, injection molding is undoubtedly the ideal choice.
4C Srl has a high range of accessories for processing molding materials such as, for example, automatic robotic presses.
Furthermore, for each order commissioned, the company guarantees flexibility and dynamism, carefully checking each finished product (previously tested).
FAQs:
- What kind of products can be made with injection molding?
- A wide range of products, from toys to automotive components.
- How long does it take to produce an object with injection molding?
- It depends on the complexity of the mold and the production quantity, but it is generally a quick process.
- Is injection molding an expensive process?
- While initial mold costs may be high, mass production significantly reduces per-unit costs.
- Is it possible to use recycled materials in injection molding?
- Yes, 4C Srl uses plastic materials from the circular economy, which with their reuse contribute to reducing the environmental impact.
- What are the most commonly used materials in injection molding?
- Polyethylene, PVC, polystyrene and ABS are just some of the commonly used materials.